The Decarb Diet: Insights into the Complexities of Supply Chain Decarbonization
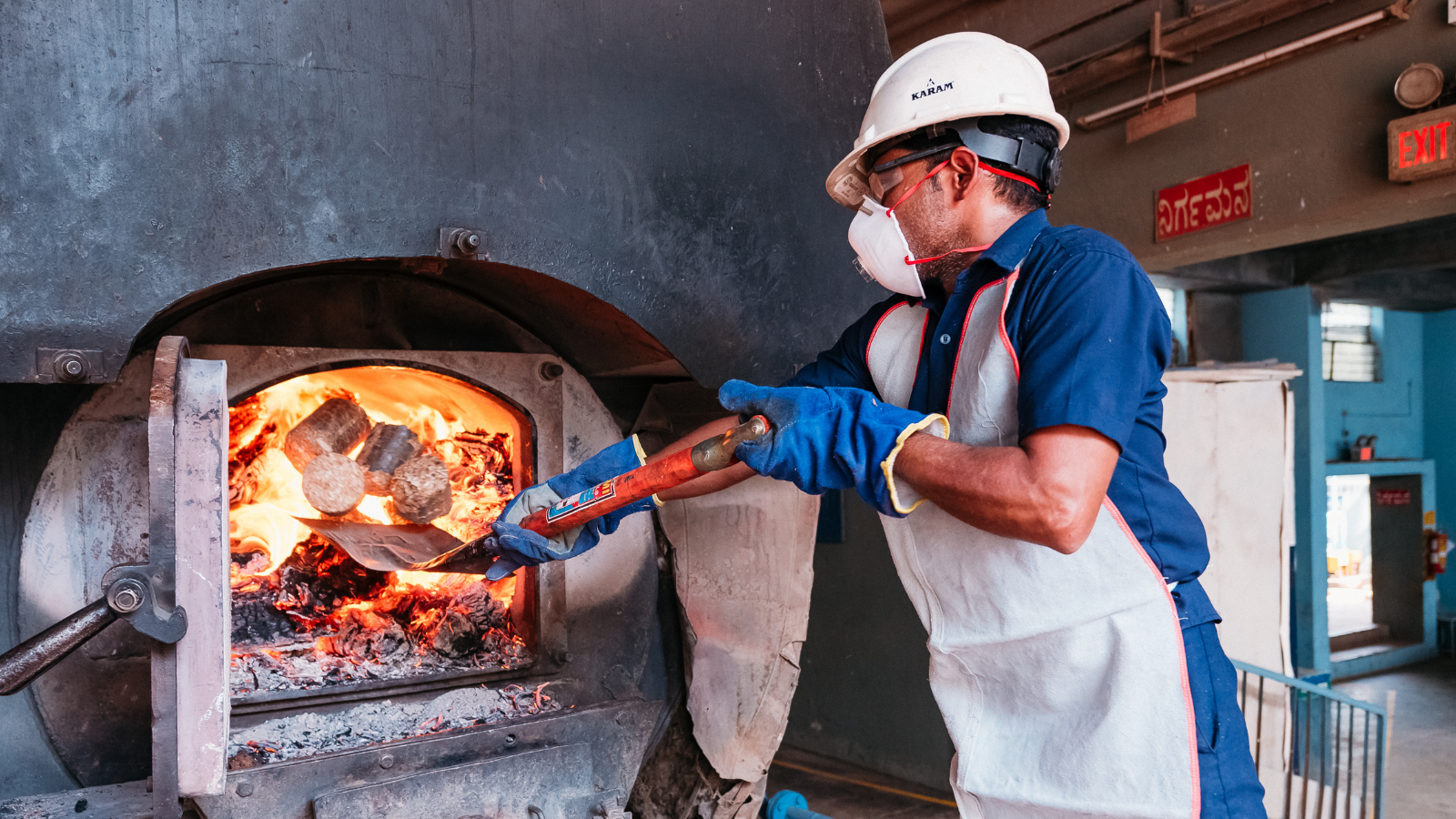
Albert Einstein famously said, ‘We cannot solve our problems with the same thinking we used when we created them.’ This insight couldn’t be more relevant in global efforts to decarbonize. For the fashion industry— responsible for up to 10% of global carbon emissions; a major problem to solve is halving its emissions in the next five years. With up to 80% of those emissions coming from supply chains, manufacturers like Shahi bear the heaviest responsibility. Accelerating progress on these fronts will require new ways of thinking and working.
How do manufacturing companies lead this transition while navigating financial risks and technological challenges?
This article explores the steps we are taking toward renewable energy and how collaboration between brands and stakeholders is key to unlocking sustainable solutions.
Breaking down energy consumption in manufacturing
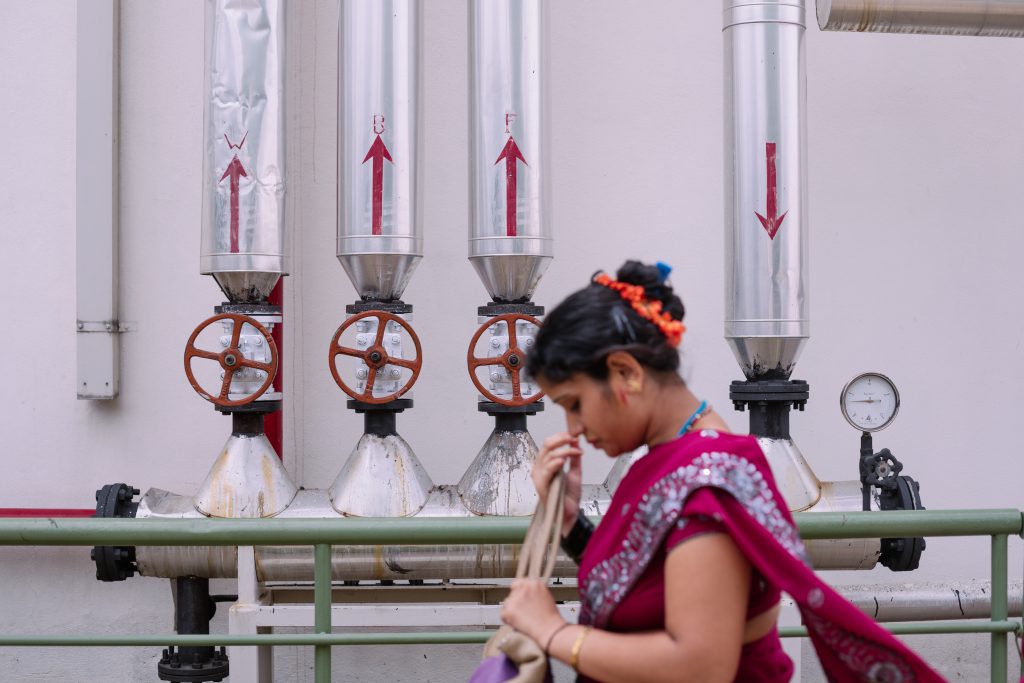
Our operations rely on two types of energy: electrical and thermal. Electrical energy powers daily activities, while thermal energy, mainly from boilers, generates steam and hot water for processes like dyeing and finishing fabrics.
At Shahi, 81% of our energy comes from thermal energy due to our large textile operations, with the rest coming from electricity. While renewable electricity has been the industry’s primary focus, phasing out fossil-fuel-based thermal energy in textile production is where the biggest impact of decarbonization lies.
Toward 100% renewable electricity at Shahi
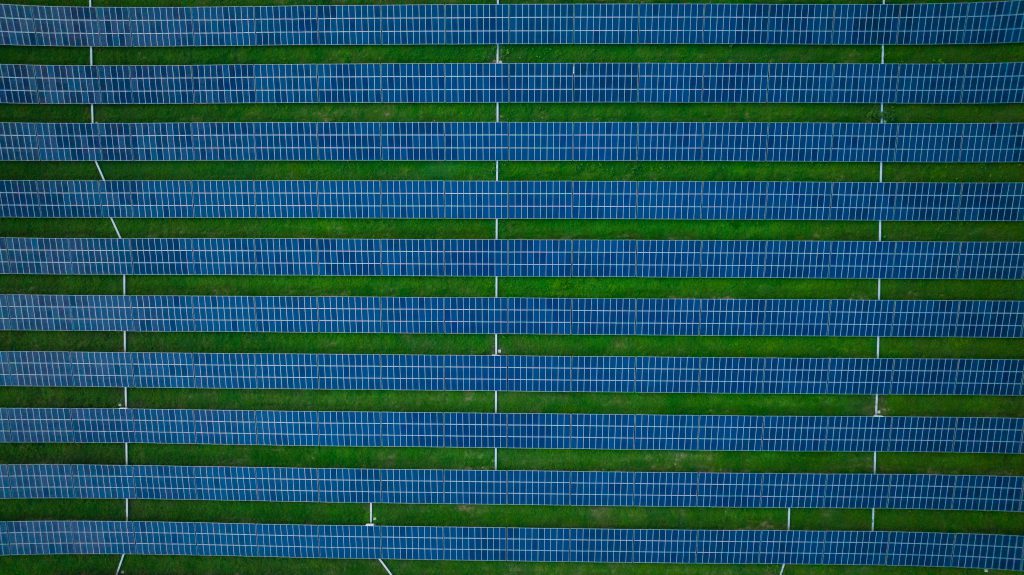
Over the past decade, we’ve invested heavily in renewable electricity, reaching 65% renewable energy for our operations. Supported by favorable government policies, in 2018, we strategically invested in two solar plants with a combined 84 MW capacity and 8.75 MW of wind power in Karnataka. These plants generate 130 million kWh annually, cutting over 600,000 metric tons of CO2 emissions since 2018. This year, we’re expanding with a 40 MW solar project in Karnataka and smaller ones in Uttar Pradesh and Tamil Nadu, bringing our renewable capacity to 151 MW.
Driven by our commitment to sustainability, we are working toward 100% renewable electricity by 2027.
Phasing out coal in our operations
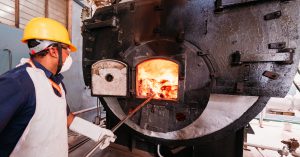
By 2022, we successfully transitioned all our garment factories from coal to biomass. The greater challenge lies in our textile mills, which require hundreds of tons of coal daily to operate. The UN The Fashion Industry Charter for Climate Action mandates that brands should not onboard any new factories and mills that use coal. This significantly accelerates the timeline for phasing out coal set by the Paris Agreement, which permits non-OECD countries until 2040. However, the Charter also states that brands should establish engagement and incentive programs to support their suppliers’ transition from coal. Thus making collaboration and a willingness to share risks essential.
We are addressing this by rapidly increasing biomass use, a carbon-neutral alternative. One of our mills has been 100% coal-free since December 2023, and two will be 50% coal-free by January 2025.
Challenges of decarbonizing thermal energy
Replacing coal with biomass as a fuel source requires substantial upfront investments from suppliers. For each of our 50 factories and 3 textile mills, we’ve invested substantially in biomass-enabled systems, including Atmospheric Fluidized Combustion (AFBC) boilers, Thermopac systems with electrostatic precipitators to capture fine particles, expanded biomass storage facilities, and automated ash handling plants to reduce health risks.
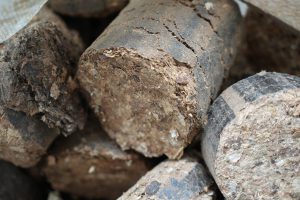
Sourcing and handling biomass also present challenges. Building a reliable supplier network is crucial to mitigate seasonal fuel fluctuations and ensure a steady supply chain. In India, like most of the world, biomass is still an informal industry compared to coal, which is well-established. To address the challenge of the biomass supply chains, we’re collaborating with biomass aggregators and experts to assess local agricultural waste availability. Our goal is to vertically integrate our biomass supply.
This, however, would be a temporary solution that will need replacing with more sustainable options, requiring additional investments in the future. We are excited by upcoming technologies such as green hydrogen, electric boilers, and heat pumps.
A study in India shows that electric boilers and heat pumps are capital-intensive and are likely to increase the cost of operations, driven by the price of electricity, which is higher than the current fuel prices per unit of energy. While the return on investment for these technologies is yet to be determined, and given that textiles is a low-margin industry, manufacturers need government and brand incentives to help switch to newer, cleaner technologies. Further, to drive emissions down further, it’s important that the national grid procures increasing amounts of clean electricity and shifts away from fossil fuels overall.
Collaboration as a catalyst for change
While the major impact of climate change lies in the supply chain, the entire value chain, including brands and other important stakeholders, must share responsibility for climate action. Collaboration with brands and stakeholders is key to reducing the risks of transitioning away from fossil fuels and creating innovative solutions that can be scaled and adopted.
First, it is crucial to accelerate R&D to find alternatives to biomass. Decarbonization isn’t just a fashion industry issue; it’s a global challenge that requires cross-industry collaboration. For example, we can learn from the tech industry, which is adopting renewables as its energy demand increases significantly with the rise of AI.
Second, sharing the financial burden requires not only brand support but also financial institutions. Manufacturers can benefit from funding for higher-risk, long-term investments, such as infrastructure changes needed for climate adaptation that go beyond debt.
Finally, reimagining suppliers as value-adding co-creators rather than just implementers ensures sustainability strategies align more closely with real-world operations.
By aligning goals, pooling resources, and fostering transparent partnerships, we can develop scalable, unified solutions to decarbonize the industry.